ONE STEP INJECTION STRETCH BLOW MOLDING (ISBM) TECHNOLOGY
One step injection stretch blow molding (ISBM) machine is an advanced and efficient plastic container blow molding equipment, which integrates injection molding, temperature conditioning (4 station unique process), stretch & blow molding, and container release processes. It can continuously produce plastic finished containers from raw materials on one machine.
Main Feature
Efficient production: One-step ISBM technology simplifies the production process, shortens the production cycle, and improves production efficiency.
Energy saving and environmental protection: The injection stretch blow molding (ISBM) machine has low energy consumption and high raw material use rate, which meets the requirements of green production.
High-quality containers: The containers produced have high precision, high transparency, and good toughness, which are suitable for high-end market needs.
High degree of automation: integrated design, easy operation, reduced manual intervention, and improved production stability and consistency.
Multi-function and multi-industry application: It can produce plastic containers of various specifications and shapes, and is widely used in sports water bottles, baby bottles, food & beverage packaging, pharmaceutical packaging, cosmetics packaging, daily chemical bottle packaging, and other industries.
Applicable to multiple materials processing: PET, PETG, PC, PCTG (Tritan TX1001/TX2001, ECOZEN YF300/T110/T110Pro), AS, PPSU, PP, etc.
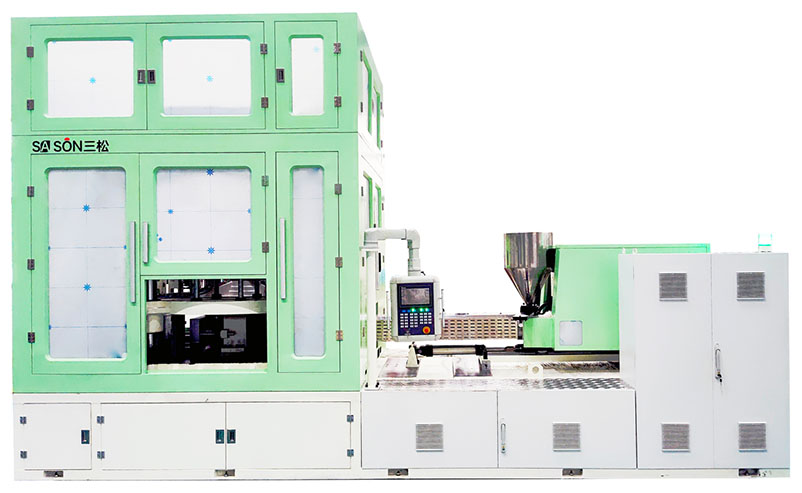
One Step Injection Stretch Blow Molding (ISBM) Machine
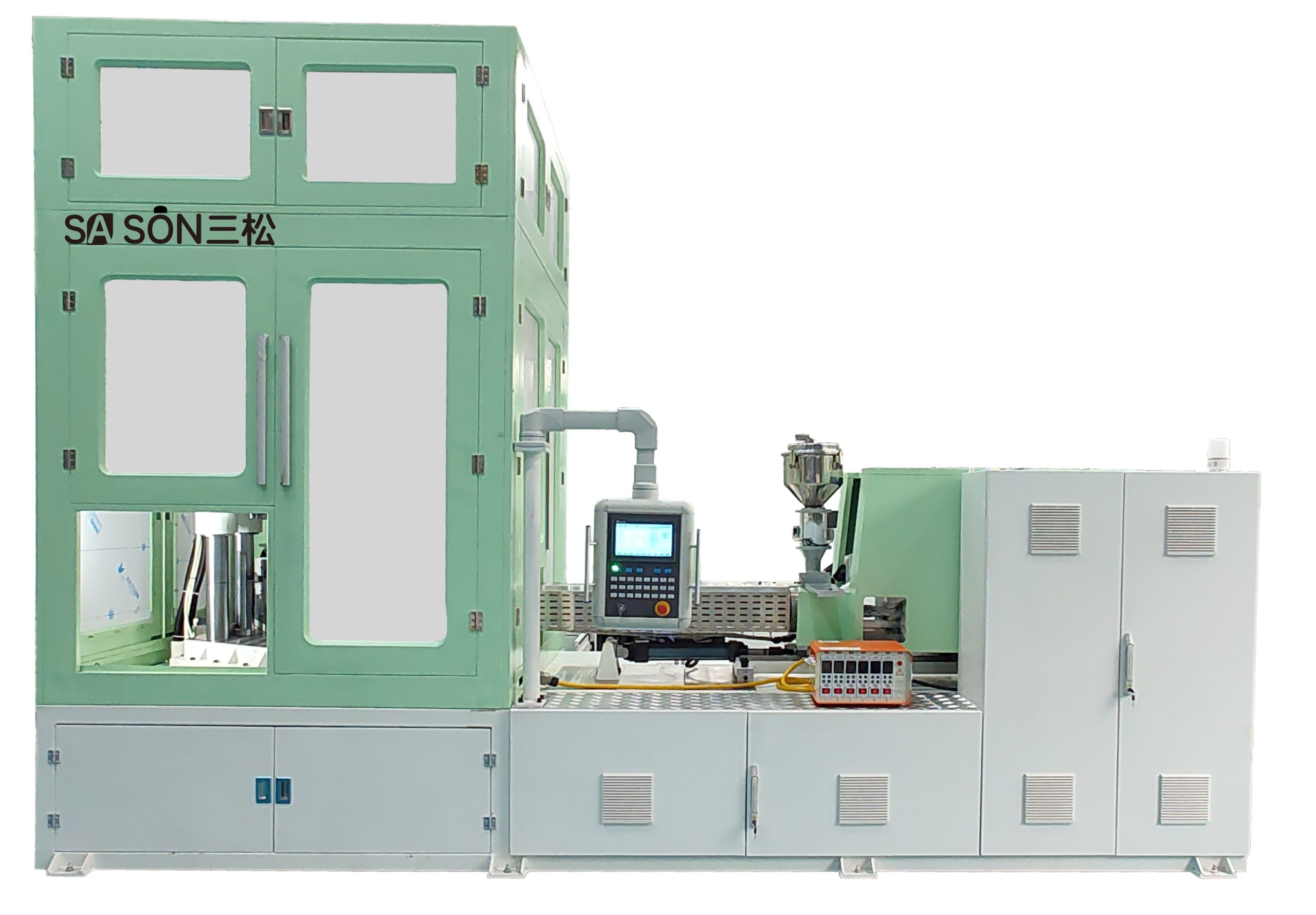
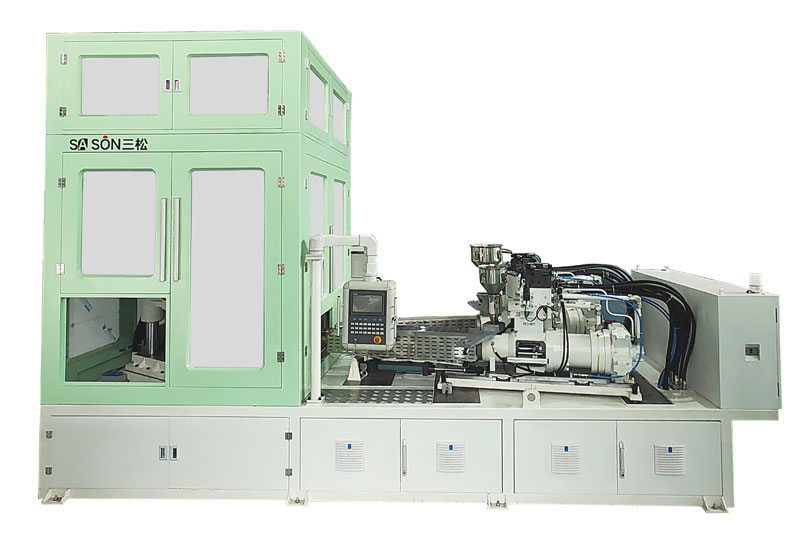
ISBM MACHINE WORKING PRINCIPLE
The one-step injection stretch blow molding machine adopts an integrated design. Through injection molding, temperature conditioning (4 station unique process), stretch & blow molding, and container release processes, the plastic raw materials are processed into finished plastic containers in one machine, reducing the deformation and damage caused by the transfer of the preforms between different equipment, ensuring the quality consistency and stability of the finished plastic containers.
Injection molding station: The plastic raw materials are heated and melted, and then injected into the preform mold to form the preform.
Temperature conditioning (4-station unique process) station: According to the process requirements, the preform is accurately heated or cooled (four-station unique process).
Stretch & Blow Molding Station: The preform is stretched in the longitudinal and transverse directions to enhance toughness and transparency, and then high-pressure air is blown to rapidly expand the preform in the blowing mold to form the finished containers.
Container release station: separate the finished containers from the mold.
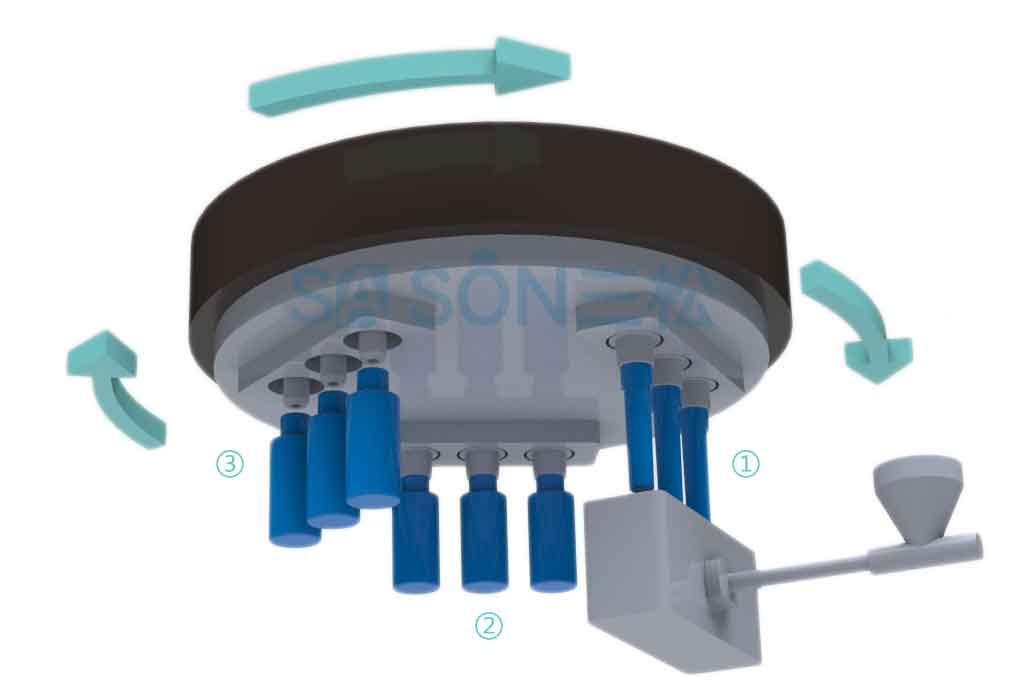
3 Station ISBM
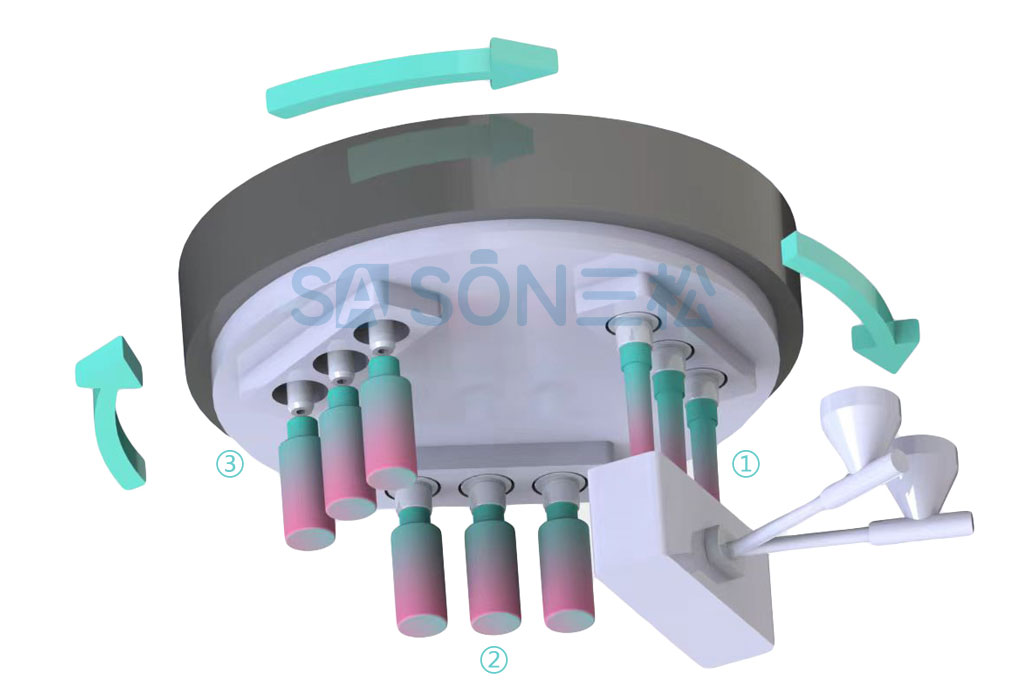
3 Station ISBM_Two Color
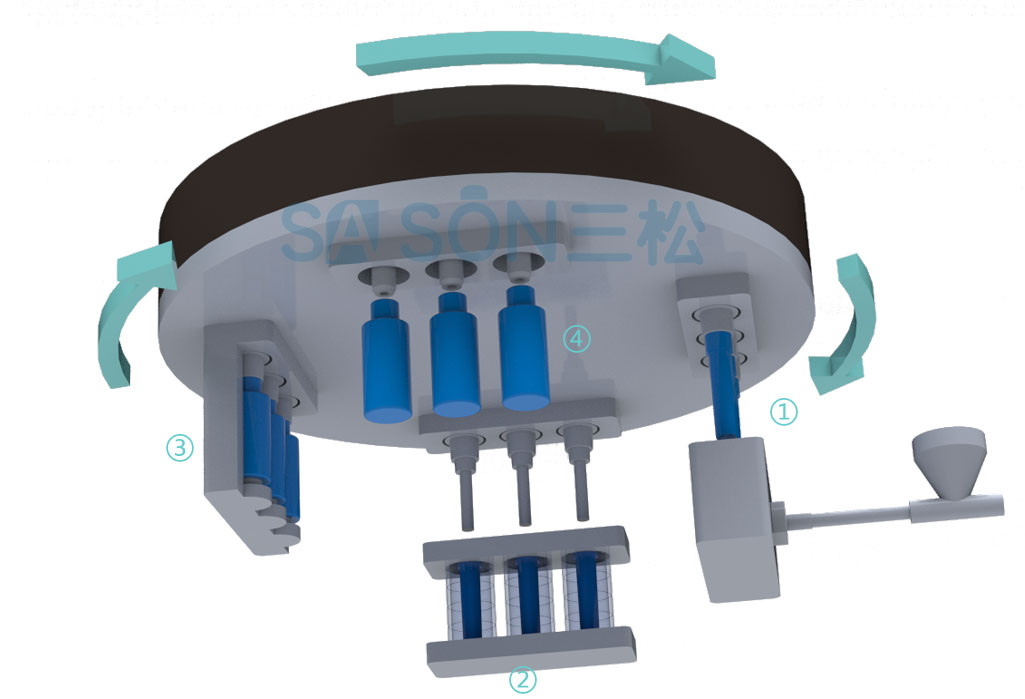
4 Station ISBM
WHY CHOOSE ONE-STEP INJECTION STRETCH BLOW MOLDING TECHNOLOGY?
The one-step ISBM technology has the following advantages over the two-step technology:
Higher production efficiency: The one-step ISBM combines the process steps of injection molding, temperature conditioning (four-station unique process), stretch & blow molding, and container release on one machine, reducing the intermediate preform cooling and heating time and improving the overall production efficiency.
Small machine footprint: The one-step ISBM requires fewer machines and occupies a relatively small area, which is suitable for factories with limited production site areas.
Stable product quality: Since the one-step ISBM process is completed continuously, it reduces the deformation and damage caused by transferring preform between different machines, ensuring the consistency and stability of product quality.
Lower production costs: The one-step ISBM reduces the number of machines and operators required, energy consumption, and site area costs, thereby reducing overall production costs.
Reduce scrap rate: Since each step in the one-step ISBM is more closely connected, the preforms are less disturbed by the outside world during the manufacturing, reducing the generation of defective and scrap products.
Simplified production management: The one-step ISBM production process is simpler, easier to operate and manage, reduces coordination issues in the process, and improves production flexibility.
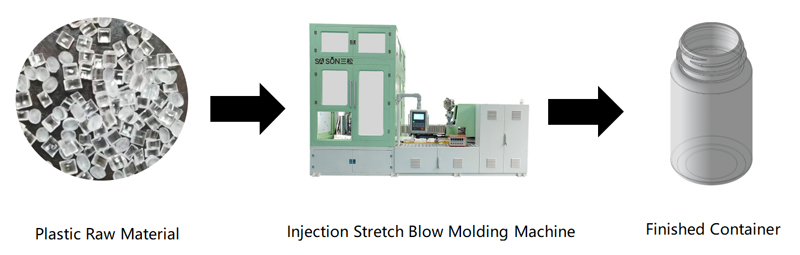